BTA-Tieflochbohrer zur internen Spanentfernung
Da die Tiefbohrstange asymmetrisch ist, weist sie eine geringe Torsionssteifigkeit auf und kann nur ein begrenztes Drehmoment übertragen. Daher eignet sich das Tieflochbohren nur für die Bearbeitung von Teilen mit Löchern mit kleinem Durchmesser. Um sich an die Bearbeitungsanforderungen komplexerer Tieflöcher mit großem Durchmesser anzupassen, entstand die Technologie des Tieflochbohrens mit interner Spanabfuhr. Da bei der internen Spanentfernung die Späne aus dem Bohrrohr abgeführt werden und die bearbeitete Oberfläche nicht abkratzen oder berühren, ist die Oberflächenbearbeitungsqualität höher als beim Tieflochbohren und auch der Durchmesserbereich der Bearbeitungslöcher ist größer.
Bohrer und Bohrstange im BTA-System sind Hohlzylinder. Das Funktionsprinzip ist wie in der Abbildung dargestellt. Die Schneidflüssigkeit gelangt über den Einlass in den Ölspender, nachdem sie unter Druck gesetzt wurde, und fließt dann durch den abgedichteten Ringraum, der durch die Bohrstange und die Lochwand gebildet wird, zum Schneidteil zur Kühlung. Schmieren Sie die Späne, drücken Sie sie in den Späneauslass am Bohrer und lassen Sie sie dann aus dem Auslass durch den inneren Hohlraum des Bohrrohrs abfließen.
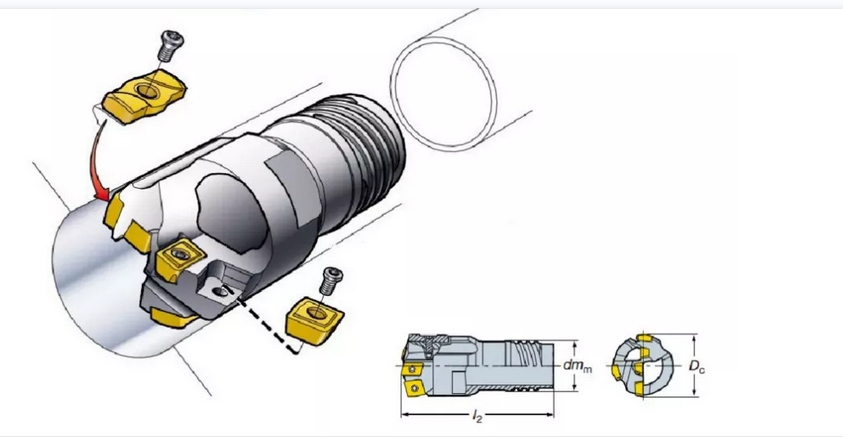
Das Tieflochbohren mit interner Spanentfernung eignet sich für die Bearbeitung tiefer Löcher mit einem Durchmesser von 20 mm oder mehr und einem Seitenverhältnis von nicht mehr als 100. Die Bearbeitungsgenauigkeit beträgt IT7~IT10, die Oberflächenrauheit der bearbeiteten Oberfläche beträgt Ra3,2~1,6 ähm, und die Produktionseffizienz liegt in der externen Spanabfuhr. Mehr als 3 Mal.
Der Hauptnachteil des BTA-Tieflochbohrens mit interner Spanentfernung: Es müssen spezielle Werkzeugmaschinenausrüstungen verwendet werden, und die Werkzeugmaschine muss außerdem mit einer Ölspäne-Trennvorrichtung ausgestattet sein, um die Schneidflüssigkeit durch Schwerkraftsedimentation oder elektromagnetische Trennung abzutrennen und zu recyceln. Darüber hinaus entsteht beim Schneidvorgang eine Hochdruckzone zwischen Werkstück und Ölspender, sodass vor dem Bohren eine zuverlässige Abdichtung zwischen Werkstück und Ölspender hergestellt werden muss.
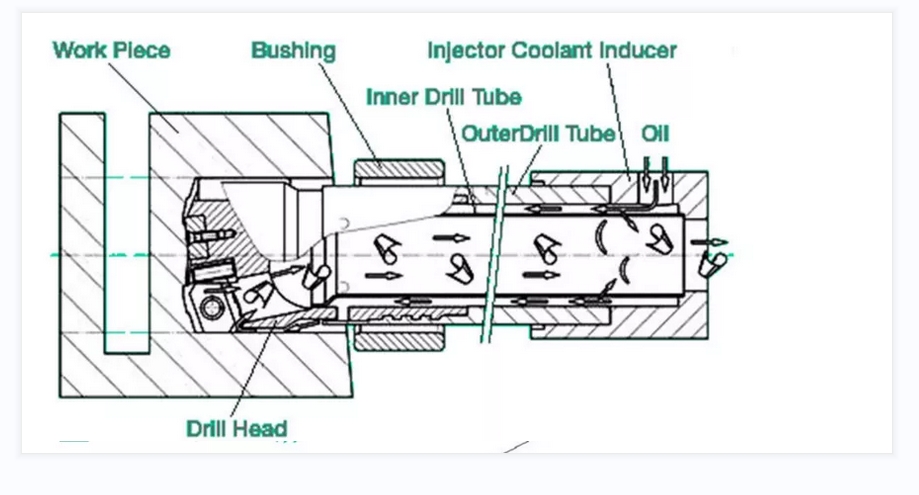
.Auswerferbohrkopf
Das Tieflochbohrsystem mit interner Spanabfuhr hat den Nachteil großer Verluste im ringförmigen Ölkanal. Während der Verarbeitung sind ein höherer Druck und eine höhere Durchflussrate erforderlich. Aus diesem Grund wurde ein Bohrsystem mit hoher Produktionseffizienz und besserer Bearbeitungsqualität auf den Markt gebracht. Technologie - Auswerferbohrkopf
Der Auswerferbohrkopf nutzt das Prinzip der Strahlsaugwirkung der Strömungsmechanik, um ein Doppelrohr-Tieflochbohrverfahren zur Spanabfuhr zu erfinden. Es verwendet zwei konzentrische Bohrstangen, um das Werkzeug über einen Stecker mit der Werkzeugmaschine zu verbinden. Das Strahlsaugbohrsystem verwendet eine doppelschichtige Rohrschneidstange, die Schneidflüssigkeit tritt nach Druckbeaufschlagung über den Einlass ein, und 2/3 der Schneidflüssigkeit gelangt in den Ringraum zwischen den inneren und äußeren Bohrstangen und fließt zum Schneidteil dient der Kühlung und Schmierung und drückt die Späne in den Innenhohlraum der Bohrstange.
Das verbleibende Drittel der Schneidflüssigkeit wird mit hoher Geschwindigkeit aus der halbmondförmigen Düse an der inneren Bohrstange in die innere Bohrstange gesprüht und bildet so eine Unterdruckzone im inneren Hohlraum der inneren Bohrstange, die eine erzeugt Saugwirkung auf die spanführende Schneidflüssigkeit. Es hat die Doppelfunktion Sprühen und Saugen. nach unten, wodurch die Späne schnell aus dem Auslass abgeführt werden.
Die Ölversorgung des Auswerferbohrkopfes erfolgt über den Drehanschluss. Der Führungssitz dient hauptsächlich der Unterstützung und muss sich nicht in der Nähe des Werkstücks befinden. Dies ist für die Fünf-Achs-Bearbeitung von großem Vorteil. Da wir bei der Fünf-Achsen-Bearbeitung in der Regel auf nicht ebene Oberflächen stoßen, darf der Führungssitz nicht nahe am Werkstück liegen. Darüber hinaus erzeugt der Strahlsaugbohrer während der Bearbeitung einen Vakuumeffekt, der eine Spanabfuhr ermöglicht und flexibler einsetzbar ist.
Der Auswerferbohrkopf eignet sich hauptsächlich für die Bearbeitung von Löchern mit einem Seitenverhältnis von nicht mehr als 100 und einem Durchmesser von 18 bis 65 mm. Die Präzision beträgt IT9 bis IT11 und die Oberflächenrauheit beträgt Ra3,2–0,8 um.
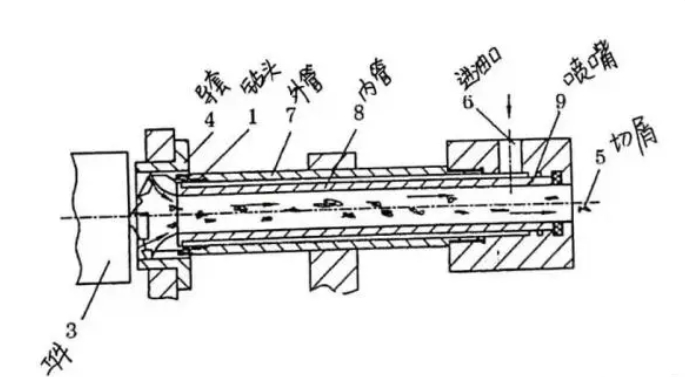
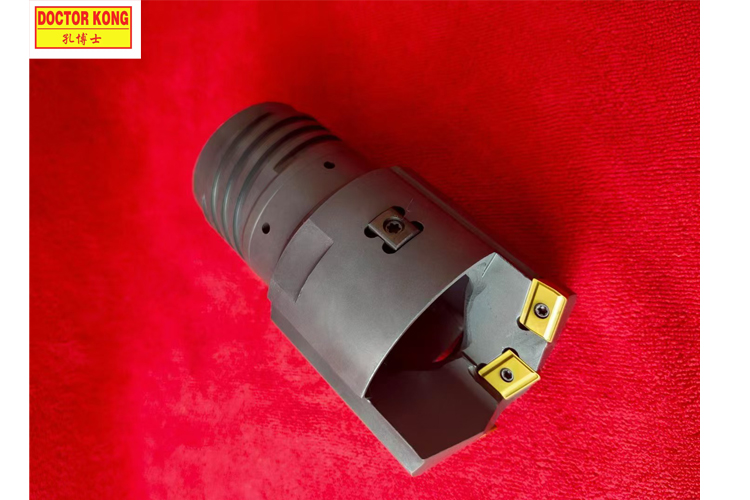
Zeitpunkt der Veröffentlichung: 07.09.2024